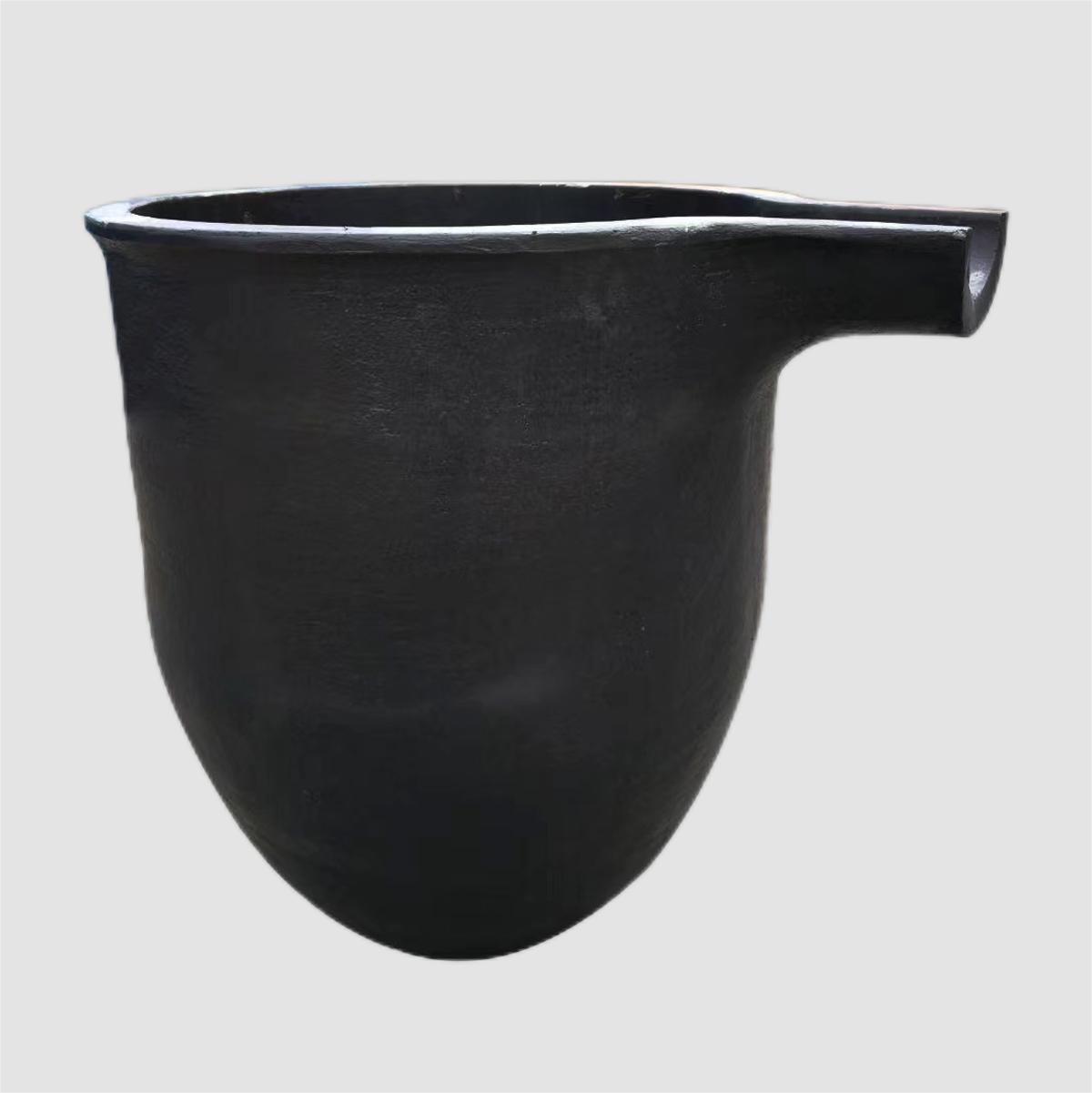
Изостатичко пресовање графитаје нова врста графитног материјала развијена 1960-их година, која има низ одличних својстава.На пример, графит за изостатичко пресовање има добру отпорност на топлоту.У инертној атмосфери, његова механичка чврстоћа не само да се не смањује са повећањем температуре, већ се и повећава, достижући највећу вредност на око 2500 ℃;У поређењу са обичним графитом, његова структура је фина и густа, а његова униформност је добра;Коефицијент топлотног ширења је веома низак и има одличну отпорност на топлотни удар;Исотропиц;Јака отпорност на хемијску корозију, добра топлотна и електрична проводљивост;Има одличне перформансе механичке обраде.
Управо због својих одличних перформанси графит за изостатичко пресовање има широку примену у областима као што су металургија, хемија, електротехника, ваздухопловство и индустрија атомске енергије.Штавише, са развојем науке и технологије, поља примене се стално шире.
Процес производње изостатичког пресовања графита
Процес производње изостатичког пресовања графита приказан је на слици 1. Очигледно је да се процес производње изостатичког пресовања графита разликује од процеса производње графитних електрода.
За изостатичко пресовање графита су потребне структурно изотропне сировине, које је потребно самлети у финији прах.Потребно је применити технологију формирања хладног изостатичког пресовања, а циклус печења је веома дуг.Да би се постигла циљна густина, потребни су вишеструки циклуси импрегнационог печења, а циклус графитизације је много дужи него код обичног графита.
Други метод за производњу графита за изостатичко пресовање је коришћење мезофазних угљеничних микросфера као сировина.Прво, мезофазне угљеничне микросфере се подвргавају оксидационо-стабилизационом третману на вишим температурама, након чега следи изостатичко пресовање, након чега следи даља калцинација и графитизација.Овај метод није представљен у овом чланку.
1.1 Сировине
ThСировине за производњу графита за изостатичко пресовање укључују агрегате и везива.Агрегати се обично праве од нафтног кокса и асфалтног кокса, као и од млевеног асфалтног кокса.На пример, изостатски графит серије АКСФ који производи ПОЦО у Сједињеним Државама је направљен од млевеног асфалтног кокса Гилсонтецоке.
У циљу прилагођавања перформанси производа према различитим употребама, чађа и вештачки графит се такође користе као адитиви.Генерално, нафтни кокс и асфалтни кокс треба да се калцинишу на 1200~1400 ℃ да би се уклонила влага и испарљиве материје пре употребе.
Међутим, у циљу побољшања механичких својстава и структурне густине производа, постоји и директна производња графита за изостатичко пресовање коришћењем сировина као што је кокс.Карактеристика коксовања је да садржи испарљиве материје, да има својства самосинтеровања и да се шири и скупља синхроно са везивним коксом.Везиво обично користи смолу од катрана угља, а у складу са различитим условима опреме и процесним захтевима сваког предузећа, тачка омекшавања коришћеног катрана угља креће се од 50 ℃ до 250 ℃.
На перформансе изостатичког пресовања графита у великој мери утичу сировине, а избор сировина је кључна карика у производњи потребног финалног производа.Пре храњења, карактеристике и уједначеност сировина морају се строго проверити.
1.2 Брушење
Обично је потребна величина агрегата графита за изостатичко пресовање да достигне испод 20 ум.Тренутно, најрафиниранији изостатски пресовани графит има максимални пречник честица од 1 μм.Веома је танак.
За млевење агрегатног кокса у тако фини прах потребна је ултра-фина дробилица.Млевење са просечном величином честица од 10-20 μ За прах од м потребна је употреба вертикалног млина са ваљцима, са просечном величином честица мањом од 10 μ. Прашак од м захтева употребу млевења са протоком ваздуха.
1.3 Мешање и гњечење
Млевени прах и везиво за смолу угља ставити у сразмери у мешалицу за загревање за гњечење, тако да слој асфалта буде равномерно пријањан на површину честица кокса у праху.Након гњечења, уклоните пасту и оставите да се охлади.
Време поста: 27.09.2023