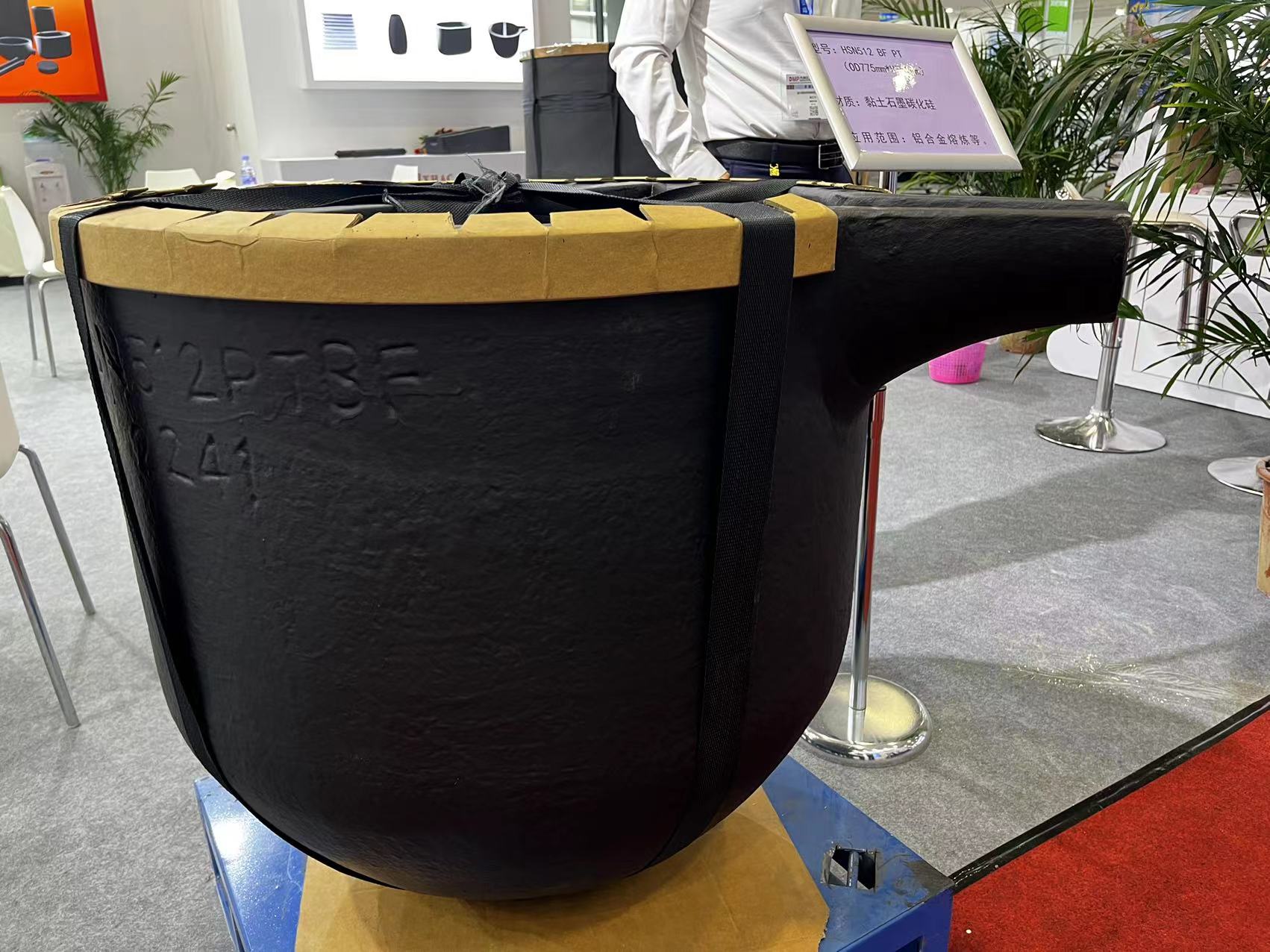
Метода припреме велике чврстоћеГрафички силицијум карбид ЦруциблеЗа метално топљење укључује следеће кораке: 1) Припрема сировина; 2) примарно мешање; 3) сушење материјала; 4) дробљење и скрининг; 5) секундарна припрема материјала; 6) секундарно мешање; 7) прешање и обликовање; 8) сечење и подрезивање; 9) сушење; 10) застакљивање; 11) примарно пуцање; 12) импрегнација; 13) секундарно пуцање; 14) премаз; 15) готов производ. Круницибилна произведена коришћењем ове нове формуле и процеса производње има снажну високу температуру отпорност и отпорност на корозију. Просечни животни век лонка достиже 7-8 месеци, са униформном и дефектуром унутрашњом структуром, високом чврстоћом, танким зидовима и добру топлотну проводљивост. Поред тога, слој глазура и премаз на површини, заједно са вишеструким процесима сушења и пуцања, значајно побољшавају отпорност на корозију производа и смањити потрошњу енергије за око 30%, са високим степеном витрификације.
Ова метода укључује област обојених металуршких ливења, посебно метода припреме високе чврстоће графите силицијум карбида за мрље од метала.
[Позадина технологија] Специјални графит СИЛИЦОН ЦАРБИДЕ ЦРУЦИБЛЕС се углавном користе у процесима ливења и ковања метала, као и у опоравку и рафинирању племенитих метала и производња производа отпорне на високе температуре и корозију и корозирање, производњу, гуму и фармацеутску производњу, као и контејнере отпорне на корозију.
Постојеће специјалне графитне силицијумне карбидне формулације и производни процеси производе производе са просечним животом од 55 дана, што је прекратко. Употреба и трошкови производње и даље се повећавају, а количина генерисана отпада је такође висока. Стога истражујући нову врсту посебног графитног силицијумског карбида и њеног производног процеса је хитан проблем за решавање, јер ови варир имају значајне примене у различитим индустријским хемијским пољима.
Да би се позабавило горе наведеним проблемима, обезбеђен је поступак за припрему графита високог снажног силицијума крстала за метално мир. Производи припремљени према овој методи отпорни су на високе температуре и корозију, имају дуг радни век и постижу уштеду енергије, смањење емисије, заштиту животне средине, еколошку стопу отпада и максимизирање циркулације и искоришћености ресурса.
Начин припреме високе строго графите силицијумске карбидне штрајкове за метално топљење укључује следеће кораке:
- Припрема сировина: Силиконски карбид, графит, глину и металик силицијун постављају се у њихове спремне састојке од стране Цране, а ПЛЦ програм аутоматски контролише пражњење и вагање сваког материјала у складу са потребним омјером. Пнеуматски вентили контролирају пражњење, а најмање два сензора за вагање постављена су на дну сваког састојака. Након вагања, материјали се постављају у машину за мешање аутоматским покретним корпама. Почетни додатак силицијумског карбида је 50% од укупног износа.
- Секундарно мешање: Након што се сирови материјали помешају у машини за мешање, оне се празни у пуфер спремник, а материјали у пуферу се подижу у спремник за мешање од лифта за секундарне мешање. Уређај за уклањање гвожђа постављен је на лифту за пражњење лифта, а уређај за додавање воде је постављен изнад компошта за мешање да би се додала вода уз мешање уз мешање. Стопа додавања воде је 10л / мин.
- Сушење материјала: влажни материјал након мешања се осуши у опреми за сушење на температури од 120-150 ° Ц да бисте уклонили влагу. Након потпуног сушења, материјал се извади на природно хлађење.
- Дробљење и скрининг: Осушени групни материјал улази у опрему за дробљење и скрининг за пре-дробљење, а затим улази у цхуртерТацк црусхер за даље дробљење и истовремено пролази кроз опрему за скрининг од 60 месх-а. Честице веће од 0,25 мм враћају се за рециклирање за даљу пре-дробљење, дробљење и скрининг, док се честице мање од 0,25 мм шаљу у резервоар.
- Секундарна припрема материјала: Материјали у пражњењу спремници се превозе натраг у машину за партије за секундарну припрему. Преосталих 50% силицијум карбида додаје се током секундарне припреме. Материјали након секундарне припреме шаљу се машини за мешање за поновно мешање.
- Секундарно мешање: Током секундарног поступка мекса, специјално раствор вискозности додаје се у спремник за мешање путем посебног решења који додаје уређај са одређеном тежином. Посебно раствор је одмерен кантом за вагање и додаје се у комппер за мешање.
- Пресовање и калупање: Материјали након секундарног мешања шаљу се на изостатско прешање машине за машину. Након утовара, сабијање, усисавања и чишћења у калупу, материјали се притискају у изостатској пресованији машини.
- Сечење и подрезивање: Ово укључује исецање висине и подрезивањем крњевих бура. Сечење врши машином за сечење за резање засећи за потребну висину, а укочене се након сечења урезане.
- Сушење: Кључића, након што се пресече и подреже у кораку (8), шаље се на пећницу за сушење, са сушењем, температура сушења од 120-150 ° Ц. Након сушења, то је топло за 1-2 сата. Пећница сушења опремљена је системом прилагођавања ваздушног канала, који се састоји од неколико подесивих алуминијумских плоча. Ове подесиве алуминијумске плоче уређују се на две унутрашње стране пећнице за сушење, са ваздушним каналима између сваке две алуминијске плоче. Јаз између сваке две алуминијумске плоче прилагођава се да регулише ваздушни канал.
- Глезање: Глазе је направљен мешањем глазура са водом, укључујући бентонит, ватросталну глину, стаклени прах, прах у праху од фелдпарта и натријум карбоксиметил целулоза. Глазура се наноси ручно четком током застакљења.
- Примарно пуцање: Крст са примењеним глазуром испаљује се једном у пећи 28-30 сати. Да би се побољшала ефикасност испаљивања, на дну пећи, на дну пећи постављен је лабиринтски кревет за пећ за бртвљење и блокада ваздуха. Кревет пећи има доњи слој заптивеног памука и изнад памука за заптивање, постоји слој изолационе цигле, формирајући лавиринтску кревету.
- Импрегнација: Пуцани лош је постављен у резервоар за импрегнацију за усисавање и импрегнацију притиска. Раствор импрегнације се транспортује до резервоара за импрегнацију кроз запечаћени цевовод, а време импрегнације је 45-60 минута.
- Секундарно пуцање: Импрегнирана лоша постављена је у пећи за секундарно пуцање током 2 сата.
- Премаз: Кључића након секундарног пуцања пресвучена је на површини на површини акрилне смоле на бази воде.
- Готов производ: Након завршетка премаза, површина се осуши, а након сушења, Цруцибле је упакована и чувана.
Вријеме поште: Мар-20-2024